Engineering
Engineering
Process Development
Optimizing your process to best meet your product specifications is one of the core competencies of Relucent. With our vast experience in a wide range of alloys, designs, and processes we can help determine the best solutions for your product and design specifications.
Product Development
Design for Manufacturability (DFM) can make the difference between a successful product launch and a constant struggle to meet technical and production deadlines. The earlier in the process that DFM is implemented, the less costly surprises later. Partnering with Relucent to create a prototype incorporating DFM is a valuable first step toward meeting your product’s demanding specifications.
Finite Element Analysis (FEA)
For particularly demanding applications, optimization of your product design can best be accomplished with the aid of finite element analysis. Our years of experience modeling medical devices will speed the development of your new medical device. Not only will the implementation of FEA bolster your product submission to the FDA, it will also reduce the number of development cycles needed–saving your company valuable time and money.
Quality & Regulatory Consulting
Our regulatory and quality personnel have a broad background of diverse expertise in submissions and quality assurance development, from product concept through product launch in both domestic and international markets. We have extensive experience in the areas of minimally invasive cardiovascular products and permanent implants, as well as topical pharmaceuticals, orthopedics, surgical and endoscopic instrumentation, glucose monitoring devices, and MRI equipment. Our team has worked with companies of all sizes from start-ups to established multinational corporations.
Process & Product Validations
Process validation is documented evidence that a product/process consistently meets predetermined requirements. The analysis of risk to the end-user (customer) is the basis for determining the stringency of these requirements. A Design of Experiment (DOE) is a useful tool to fully understand the inputs and outputs of a process prior to starting a process validation. A DOE is a methodical approach to define statistically significant factors that affect the critical outputs of a process. Our team can assist with designing future process and product validations, or retroactively validating a process that is already in place.
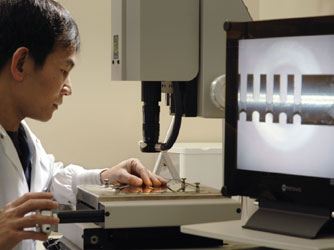
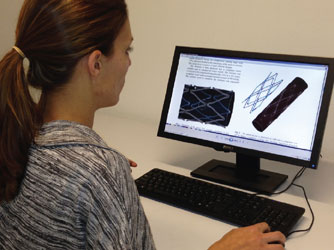
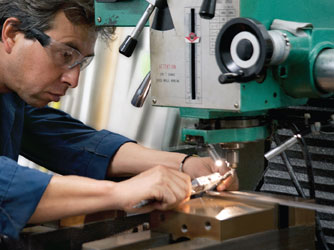
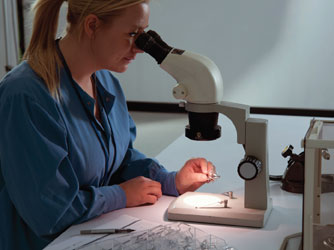
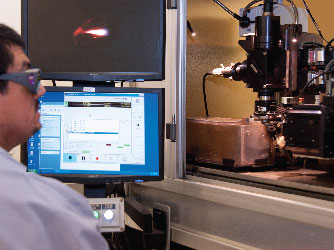
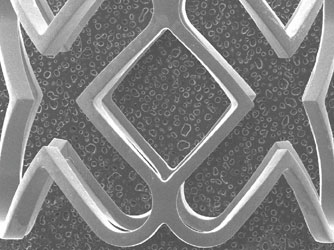